THE IMPORTANCE OF WELDING FUME EXTRACTORS: PROTECTING YOUR HEALTH IN THE WORKSHOP
Welding fume exposure is closely regulated because of the negative health and safety risks associated with it. The particulate matter found in welding fumes can include harmful metals and gases such as argon, nitrogen, carbon dioxide, carbon monoxide, and hydrogen fluoride.
Workplace conditions, safety measures, and the way that machine processes are performed are the responsibility of the employer. Complying with OSHA, AWS and NIOSH guidelines ensure the health and safety of your employees.
Weld fume extractors capture harmful fumes, gases, smoke, and other airborne contaminants at, or near, source points to help machining facilities meet regulations and keep employees safe.
WHAT IMPACTS WELDING FUME EXPOSURE?
1. The type of welding that takes place
2. Ventilation and extraction processes
3. The welder's working methods
4. Air pattern and movement
5. Welding rod composition
6. Where the welding takes place - indoors/outdoors
To ensure the safety of machine operators, it's critical to implement fume extraction systems in environments where welding equipment is being operated. Employers and machine operators must remain current and abide by manufacturer safety and operation manuals.
When selecting a weld fume extraction system, it's important to identify the work practices, hazards, and consumables of welding applications in your facility to keep exposure at or below an acceptable limit. To guarantee effectiveness, weld fume extraction systems must be appropriately used and positioned based on the machining process and application.
Weld smoke and fumes are a leading source of air contamination in metal fabrication facilities. Without a way to control and capture these pollutants, there's a raised concern for health and safety.
Fume extraction systems are used to control overexposures to the fumes and gases that develop during welding and cutting. An adequate fume collection system will prevent exposure by keeping dangerous contaminants below the acceptable limits. When choosing a welding fume extraction system, it's important that it's designed and built to accommodate your application demands.
TOP 4 WELD FUME COLLECTION METHODS
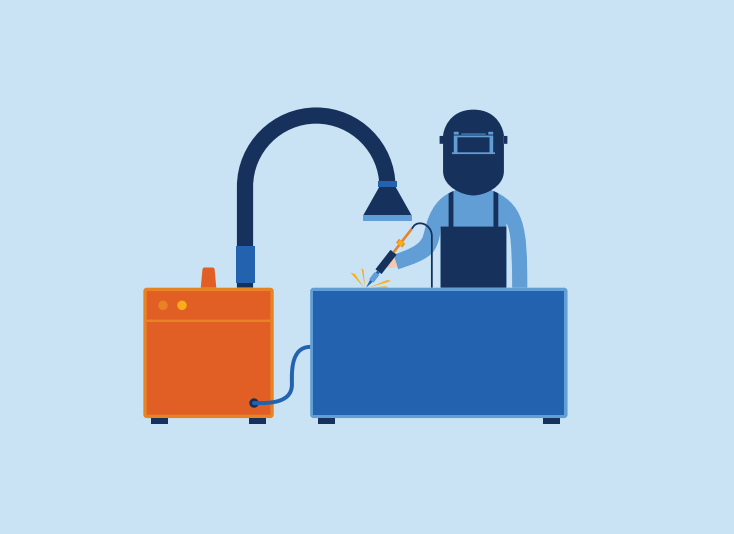
1. PORTABLE FUME EXTRACTORS
A fume arm (snorkel) attaches to a blower and filter inside of a frame with casters
Pros |
Cons |
✓ Affordable and fast
✓ It's easy to buy more portable fume extractors when needed
✓ The fume arm must be positioned at the center distance to be effective. This means the operator will be moving the fume arm as they move around the project |
• Only so much filter media fits inside which means that filter changes are required more frequently when compared to other methods.
• If the fume arm isn't used correctly, weld fume exposure is still an issue. |
2. SELF-CONTAINED DOWNDRAFT TABLES
Self-Contained downdraft tables pull air into a frame with a blower and filters that are located inside of the table.
Pros |
Cons |
✓ Mid-range price, doesn't cost much more than a portable depending on the table size
✓ The safest possible solution
✓ Can be used for both welding and grinding
✓ Minimal installation requirements
✓ Requires little operator involvement, they simply need to make sure the unit is turned on
✓ Easy to purchase and add more tables as your business grows
|
• The height is set which can be troublesome for tall or short operators.
• The application must be bench welding.
|
EMPTY DOWNDRAFT TABLES
Empty downdraft tables are unpowered and ducted and rely on a central dust collector or fume extraction system to pull the air down away from the operator and into the external collector.
Pros |
Cons |
✓ Flexible and customizable workstation
✓ Can be connected to any central dust collector or fume removal system
✓ Can be custom fabricated to meet application requirements
|
• Ductwork adds installation costs.
• Not easy to expand with business growth.
• The welding area is relatively permanent, you will not be able to move units easily without significant expense.
|
3. CENTRAL DUST COLLECTORS
Ducted to fume arms (snorkel) or "empty" downdraft tables.
Pros |
Cons |
✓ All filters are at the central dust collector making maintenance easy
✓ Filters will only need to be changed once a year or longer (if properly sized)
✓ Lowers total cost of ownership |
• Not easy to expand, the weld area must be determined and accounted for ahead of time for growth.
• The welding area is relatively permanent. You will not be able to move units easily without significant expense.
• High initial costs.
|
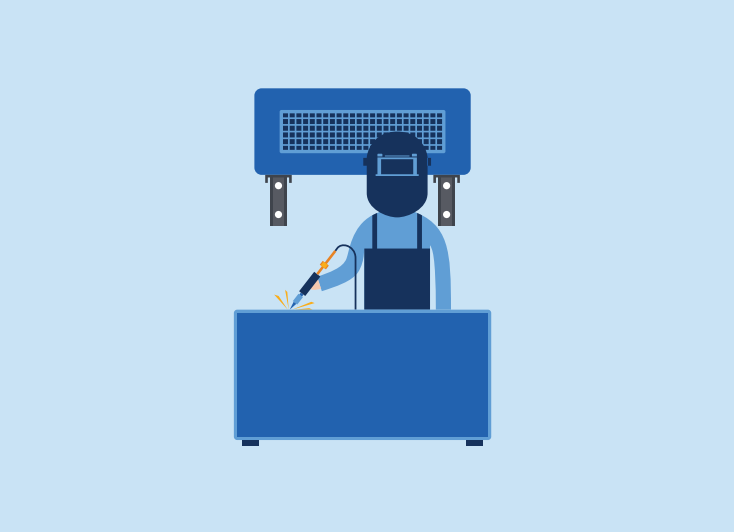
4. AMBIENT AIR CLEANERS "PUSH, PULL"
A central dust collector with duct, or several ambient air cleaners.
In environments where welding processes are performed, ambient air cleaners work as a secondary system to extract what isn't removed by the primary collection solution.
Pros |
Cons |
✓ An affordable & fast solution
✓ Cleans ambient air
✓ Best used when parts are very large and source capture is impractical, Ex: trailer manufacturing |
• Filter changes can be difficult because these units are installed/ mounted 12-14 feet off the floor.
• Operators are exposed to fumes as they pass their breathing zones on the way up.
• Not an ideal solution for at-source capturing.
|
WHAT TO ASK WHEN CHOOSING A WELDING FUME EXTRACTOR
The first thing to know about choosing a fume extractor is that it will vary depending on your application demands. When metals and alloys are welded, toxic fumes release into the airstream and settle on floors and surfaces raising the risks of employee injury and equipment malfunction.
The fume and gases produced from welding and other machining processes must be captured and controlled to ensure a safe and risk-free working environment.
Without a way to control and capture these contaminants, there is an increased risk of health and safety injuries and production loss - which is why it's important to collect fumes as close to the source as possible using a fume extraction system.
Welding fume extraction systems capture and filter dangerous fumes, smoke, and other airborne contaminants before they reach breathing zones. It's crucial to choose the proper fume extractor for your specific application but before you do, here are questions you should ask!
HOW BIG IS YOUR FACILITY OR WORKSHOP?
The type of fume extractor and the number of systems required for your application will vary based on how much floor space and wall space you're working with. Facilities that have machining processes confined to a specific area or have limited floor space may benefit more from a fixed system - while applications, where adaptability is required, may benefit more from a flexible system.
HOW MUCH WELDING TAKES PLACE?
Based on how many hours per day/month that welding or other machining processes take place will determine what type of fume extractor meets your requirements.
If welding is only done occasionally in your workplace, you may prefer lighter portable units that offer flexibility and can easily be stored. If you're working in a facility where welding takes place 8+ hours a day, you may prefer fume extraction systems that provide longer filter lives and are self-cleaning.
WHAT REGULATIONS NEED TO BE MET?
Remain current on OSHA, NIOSH, state, and local regulations to ensure that your facility or workshop meets standards.
For example, according to NFPA 484, it is against OSHA standards to utilize a dry downdraft table for combustible dust control (such as Aluminum or Titanium). A wet downdraft table is required in any facility where explosive dust is present.
DOES THE FILTER MEET YOUR APPLICATION REQUIREMENTS?
It's critical to choose a fume extraction system that comes equipped with a filter that's capable of meeting your application demands. The proper filter configuration prevents issues like frequent filter changes, filter overload, and equipment malfunction.
DOES THE FUME EXTRACTOR OFFER FLEXIBILITY?
If applications or machining processes involve metals that can create explosive dust, such as aluminum, magnesium, titanium, a wet downdraft table is right for you. To keep combustible dust controlled, it has to be captured at the source.
IS THE FUME EXTRACTOR USER-FRIENDLY?
Flexibility is key in the comfort and efficiency of machine operators. Fume extraction systems that provide smooth articulation are easier to move around work projects, or out of the way when not needed
If you're working in a small space or a shop where machining isn't frequent you might benefit from a portable fume extractor. If you're working in a large facility, or in a facility where machining is frequent, you may be interested in a larger or fixed fume extraction system.
DOES THE FUME EXTRACTOR MEET YOUR REQUIRED AIRFLOW?
Fume extraction systems must meet the CFM requirements of your application. There is a range of things that impact the airflow required by a machining process - for professional assistance, get in touch with our team of experts.
Fume Xtractors was developed to combat the health hazards that industrial machine operators are faced with on a daily basis. We offer a dynamic selection of equipment to accommodate facilities where welding and other machining processes take place, or where explosive dust is present. Protect your work environment with a solution from Fume Xtractors!
You may also like:
• Why Is Welding Fume Removal Important?
• The Dangers of Zinc Fumes in Welding
• Hex Chrome in Welding